New Age Tool and Die Shop: Embracing Cutting-Edge Innovations
- buddyb2
- Dec 17, 2024
- 3 min read
Updated: Apr 8
Tool and die technology has dramatically changed over the years, transitioning from basic handcrafting to sophisticated innovations that drive modern manufacturing processes. This blog post explores the historical journey of tool and die technology, highlights innovative trends shaping its future, and discusses how digitalization and automation are impacting the industry.
Historical Overview of Tool and Die Shops
The story of tool and die shops begins with early artisans using simple stone and metal tools to create essential items. As societies settled and evolved, the need for advanced tools grew substantially. By the Middle Ages, skilled blacksmiths were producing an array of tools that enhanced efficiency in construction, agriculture, and various crafts.
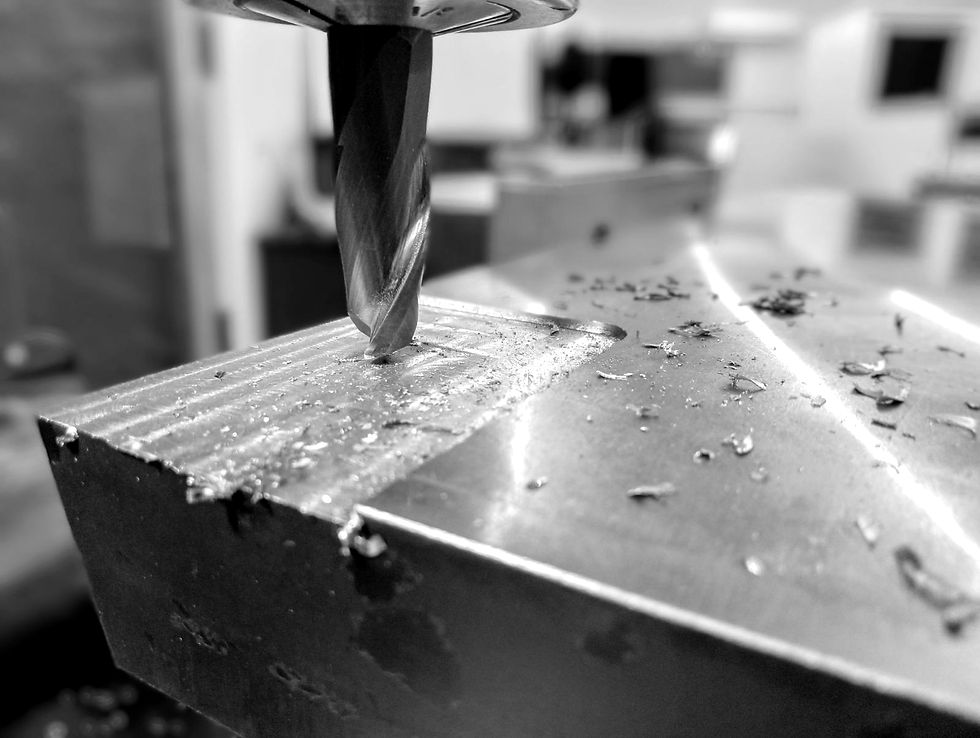
The Industrial Revolution in the 18th century marked a critical turning point. With the arrival of steam power and mechanization, industries needed tools and dies that were more precise and durable for mass production. Specialized craftsmen emerged, establishing tool and die shops dedicated to producing these essential components.
The 20th century brought even greater changes with the introduction of computer numerical control (CNC) machining. CNC technology significantly improved precision in manufacturing, minimizing human error and enabling the production of intricate geometries. For instance, progressive die stamping manufacturers now rely heavily on wire EDM (electrical discharge machining) machines for creating complex shapes from advanced hardened metals, allowing for quicker and more precise die components.
Over the decades, the evolution of tool and die technology has mirrored broader societal and technological advances, transforming from simple hand tools to today’s automated systems equipped with smart technology.
Innovative Technologies Shaping the Future

As we enter the 21st century, several cutting-edge technologies are redefining the tool and die industry. One key trend is the rise of additive manufacturing, often referred to as 3D printing. This technology enables manufacturers to produce complex designs and prototypes much faster—reducing lead times s and decreasing material wastage.
Another notable advancement is the growth of smart manufacturing through the Internet of Things (IoT). Tools equipped with sensors can monitor their performance in real-time, providing valuable data on wear and tear. This feedback not only enhances maintenance practices but also increases the lifespan of tools and even machines.
Incorporating artificial intelligence (AI) into the design and production phases is also gaining traction. Machine learning can process data to optimize designs, decreasing production times while minimizing waste.

Furthermore, automated programming interface (API) have continued to evolve enabling repeatable results when programming these complex machines readily available to a tool and die shop. The interface controlling these modernized machines is continually improving by creating a user interface that is adaptable to most tool and die shop's everyday tasks. From the design software to programming software, API is being used for repetitive tasks during design and building so that the tool and die designers/makers can focus on key areas of their project not fully benefitting from API at this time.
Impact of Digitalization and Automation

The digital revolution is fundamentally transforming tool and die technology. Digitalization enhances communication and collaboration within manufacturing, allowing seamless coordination among design, production, and quality control teams.
Automation enhances productivity and minimizes errors. Automated systems operate continuously, executing repetitive tasks with a level of precision beyond human abilities. Every automated process generally results in substantial cost savings for both businesses and their customers.

Digital twins—virtual replicas of physical tools and dies—are also gaining traction. These models enable manufacturers to simulate processes and perform predictive maintenance, optimizing systems without physical alterations. Companies utilizing digital twins have reported a significant timesaving in design modification processes.
While automation and digitalization offer extensive benefits, challenges remain. Adopting new technology requires significant investment in both systems and employee training. Concerns about job displacement also exist, as traditional tasks may be replaced by automated solutions.
Looking Ahead
The evolution of tool and die technology highlights humanity's creativity and resilience. From its humble roots to its current state of advanced innovation, this industry continues to adapt in an era of rapid technological advancement. The future holds promise, with emerging technologies like 3D printing, IoT, AI, and digital twins leading the way for increased efficiency, accuracy, and creative possibilities.
As the industry progresses, finding a balance between the advantages of automation and the necessity for skilled labor will be critical. Continuous learning and adaptation will define the next chapter in the evolution of tool and die technology.
Understanding these shifts offers crucial insights into a vital aspect of manufacturing and inspires the next generation of engineers and manufacturers. Their role in pushing the limits of possibility will be essential for future advancements in this field. Embracing these advancements will shape the future of production for years to come.
Comments